FRANCK BOCCACCINI
Consultant en fabrication & chef de projet industriel
Un parcours riche qui a débuté en 1990 comme opérateur programmeur régleur CNC qui s’est poursuivi dans les métiers d’industrialisation et enfin comme directeur de production avec pour fil conducteur l’analyse et la maîtrise des procédés de fabrication.
Domaines de compétences :
– Direction de production
– Supply chain
– Industrialisation
– Exploitation d’atelier
– Réglages machines
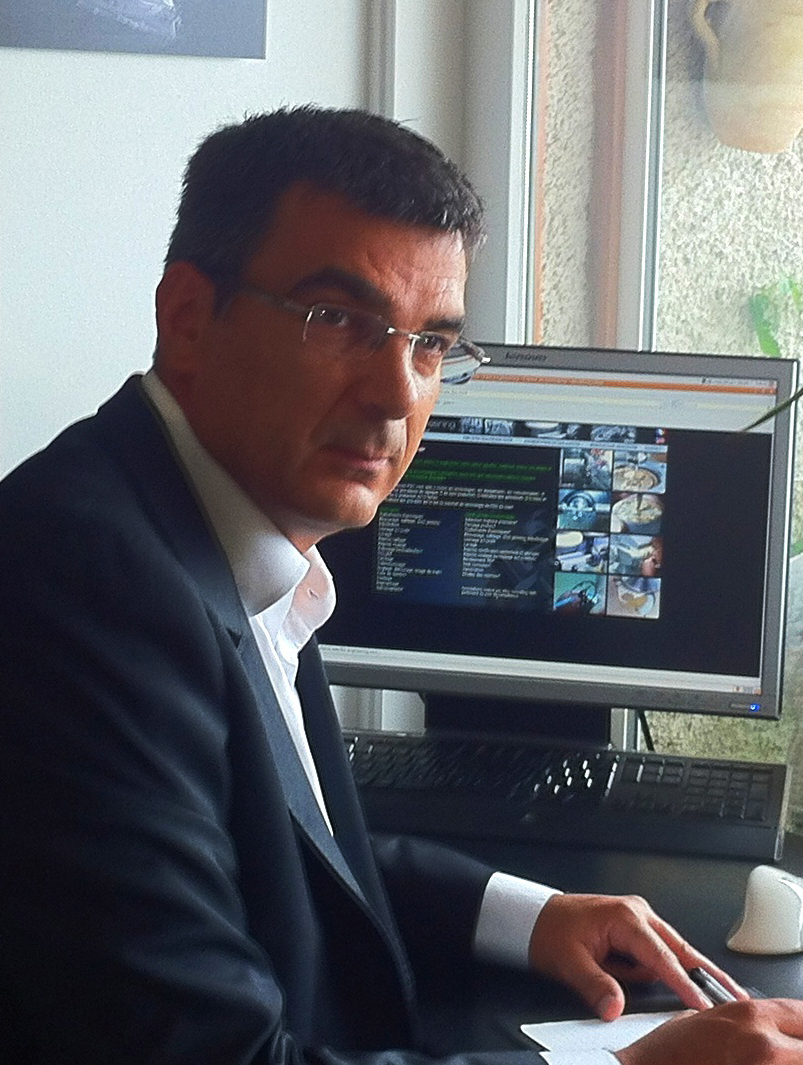
POLE DE COMPETENCES
Véritable force de frappe pour résoudre les problèmes pointus d’usinage.
FBO Engineering anime un pôle de compétences usinage qui a pour but d’apporter des solutions d’usinage performantes et fiables aux clients.
Le pôle de compétences est composé de partenaires leaders sur leur marché qui apportent matériel et savoir faire de haut vol.
Notre actualité :
Les solutions d’usinage dans les matériaux difficiles à usiner. Notamment les matières sans apport soufré, ni plomb.
Notre méthode :
Essais qualificatifs : nous testons rigoureusement tous les outils, huiles, paramètres sur les meilleures machines du moment pour réaliser une pièce et une matière choisie. Nous qualifions les matériels qui ont atteint les meilleurs performances de qualité, de durée de vie et de vitesse pour un usinage en continu 24H/24H.
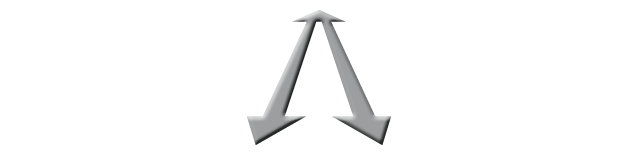
LES CLIENTS
Les entreprises qui ont fait confiance à FBO Engineering
Domaine médical
ARTICLES DE PRESSE
Voici un article paru le 08 mars 2018.
Une méthode de réglage qui améliore la productivité des tours.
Franck Boccaccini intervient auprès des entreprises de décolletage pour aider les régleurs à produire des pièces bonnes du premier coup.
Pour cela, il a rédigé plusieurs règles de travail, fruit de près de 30 ans d’expérience dans l’usinage, qui va éliminer tous les aléas de la production.
Si aujourd’hui, les régleurs de l’entreprise de décolletage DGC, à Magland (Haute-Savoie), se sentent plus en confiance dans leur métier, sont plus sereins quand ils laissent tourner leurs machines-outils la nuit, sans surveillance, ils le doivent à un homme, Franck Boccaccini. Ce Suisse de 51 ans a passé une trentaine d’années dans l’industrie, avant de fonder, à Genève, son cabinet de consultant, FBO Engineering.
Ayant occupé la fonction d’opérateur-programmeur-régleur CNC, puis des postes dans les métiers de l’industrialisation, avant de terminer cette première partie de carrière comme directeur de production, Franck Boccaccini a toujours eu le goût pour l’analyse et la maîtrise des procédés de fabrication. « Dans mon parcours professionnel, j’ai toujours eu cette proximité avec l’usinage et l’amélioration des procédés, confie-t-il. Et c’est à travers cette expérience-là, que j’ai pu peaufiner ma méthode. J’ai pu comprendre les enjeux, de par ma position de directeur de production, et j’ai pu en définir les méthodes comme si j’étais un ouvrier. »
En fondant FBO Engineering, cet ancien responsable de l’industrialisation chez Derendinger, une entreprise suisse qui fabrique des pièces mécaniques de haute précision pour l’aviation, a souhaité partager sa méthode afin « d’apporter des solutions d’usinage performantes et fiables aux clients ».
Sa méthode ? « Remplacer la variabilité des processus d’usinage par des réglages de précision simples et accessibles à tous », résume-t-il.
Le centrage Y
Et de prendre pour exemple le centrage Y des outils. « L’influence sur la durée de vie des outils du centrage Y, c’est la partie variable d’un tour, c’est, par conséquent, la quantité d’erreurs laissée au centrage. » Pour Franck Boccaccini, l’idée est d’enlever toutes ces variables d’usinage par des réglages factuels et simples. « Cela démontre qu’un réglage de précision stabilise la partie variable d’un processus, et du coup, le processus ne varie plus durant la production », insiste-t-il.
Et d’ajouter que « plus vous avez d’outils à régler, plus ce sera important d’avoir un réglage de précision. Si vous avez votre machine montée comme un sapin de Noël, vous allez avoir un feu d’artifice d’aléas de production, si vous ne pra-tiquez pas la méthode qui assure la reproductibilité. Au lieu de subir, vous allez garantir des temps où il ne se passera rien, c’est-à-dire où vous n’allez rencontrer aucun pro-blème ». Second exemple : une opération de fraisage sur un tour. « Si vous laissez du mal-rond, certaines dents de votre fraise vont être surchargées tandis que d’autres seront sous-chargées. Les dents surchargées vont finir par casser avant la fin de la durée de vie de l’outil, les autres généreront de la bavure. J’ai une méthode pour régler les outils de fraisage en tournage. »
Au total, ce sont huit procédures de réglage que propose le consultant genevois. Cela va du réglage canon, au centrage Y, en passant par la coupe au panier. A cela s’ajoutent trois règles de programmation de la CN : anti-bavure, anti-surcharge et anti-accumulation de copeaux.
« On va décider les parcours d’outil qui n’engendrent pas d’accu-mulation de copeaux, de surcharge -let de bavure. La solution se trouve dans le choix du parcours d’outil, et j’apporte les règles à respecter pour créer ces parcours d’outils », décrit Franck Boccaccini.
« Au début, j’étais sceptique »
« Au début, j’étais sceptique, témoigne Gaël, régleur chez DGC. Nous faisions les centrages Y, mais ils n’étaient pas aussi précis que la méthode de FBO. Ce sont des règles logiques, qui demandent de passer plus de temps en amont d’une pro-duction, mais on y gagne ensuite. Désormais, nous n’osons plus com-mencer une série de pièces avec un outil mal réglé. » Pour Gaël, la méthode a apporté « un sentiment de sécurité ». « On remplace quelque chose d’approxi-matif par quelque chose de 100% reproductible », ajoute l’expert suisse. « Cela nous a permis de faire tourner nos machines la nuit sans sur-veillance, enchaînent Eric et Grégory, deux autres régleurs de la société. C’est un pas à sauter et grâce à la méthode FBO nous avons franchi cette marche-là. »
Pour l’ancien responsable de la production de l’horloger Roger Dubuis, à Genève, appliquer sa méthode entraînera plusieurs conséquences favorables dans la vie d’une entreprise d’usinage. Et d’en énumérer quelques-unes : produire des pièces sans rebus, avec un TRS de 90% toujours atteint, supprimer les listes de non-conformité client et toutes les actions correctives qui en découlent, plus besoin de postes de tri, de Six Sigma, d’ordonnancements compliqués, de GPAO, la fin des relances et retards planning dus aux non-conformités et aux aléas de production, et de ces projets spécifiques de résolution de problèmes très consommateurs de temps.
« 21 heures de pièces bonnes par jour, c’est le minimum garanti par FBO pour ceux qui veulent bien appliquer ma méthode », De fait, quand le consultant débarque chez un nouveau client, il a pu constater une certaine agitation. « Les gens sont tous débordés, dit-il, à cause des problèmes de retards, d’ordonnancements, de retouches… » En résumé, le sous-traitant ne subira plus les consé-quences de tous ces aléas de production.
Des pièces sans bavures
Désormais, Gaël est un décolleteur plus épanoui dans l’atelier. « Une heure de réglage sur ma machine me permet d’être tranquille pendant 17 heures, assure-t-il. C’est devenu un confort, cela a facilité mon travail. La méthode m’a apporté plus d’envie dans mon métier. Elle m’a remotivé. » Et de montrer au journaliste une pièce. « C’était un nid à bavures, maintenant je parviens à l’usiner sans la moindre bavure. Certains décolleteurs déclinent les pièces en Peek, car c’est une matière qui fait trop de bavures. En appliquant ma méthode sur la coupe au panier, vous n’aurez plus de bavure », enchaîne Franck Boccaccini.
Gaël témoigne à nouveau : « J’ai une pièce qui tourne en ce moment. Avant, j’étais toujours sur mon tour pour tirer les copeaux, contrôler les cotes. Alors que maintenant, je n’ai plus les problèmes de copeaux grâce aux règles de programmation, et je n’ai plus de variation sur les cotes, car les réglages de base ont été bien effectués. »
Autre témoignage avec Eric et Grégory. « Chaque régleur applique à sa façon les méthodes de réglage, qui n’étaient pas toujours académiques, analysent-ils. Mais surtout qui n’avaient pas la même répétabilité que celle de FBO. Tandis que maintenant, toutes nos machines sont réglées de la même façon, quel que soit le régleur qui travaille dessus. » Et à Franck Boccaccini de conclure que « le savoir-faire d’une entreprise est pérenne à partir du moment où il règne un esprit d’équipe qui s’appuie sur les mêmes règles ».
Jérôme Meyrand
Franck vu par les autres…
Il n’est jamais facile de parler de soi c’est pourquoi en tant que ami et webmaster de Franck Boccaccini, je me devais de rédiger ces quelques lignes…
Franck s’exprime autant dans son milieu professionnel que dans les sports de glisse qu’il pratique avec passion : le snowboard et le windsurf. En sport, mon pote est un stupéfiant et rare mélange de puissance (que son gabarit lui permet) et de finesse. Cette finesse provient de sa capacité à analyser tous les paramètres entrant en jeu dans la pratique de ces sports complexes : son corps, les mouvements à produire et aussi l’interaction de tout ceci avec son matériel ainsi qu’avec le support sur lequel il évolue.
Les courbes que Franck grave dans la neige ou les sillages qu’il laisse derrière lui dans l’eau sont parfaits. Tout comme ses programmes de parcours d’usinage métal ou inox : ils sont purs, propres et toujours calculés par anticipation. En effet, Franck est doté d’une très grande capacité de calcul des mouvements mécaniques ainsi que de la gestuelle du corps. Cette faculté lui permet d’être plus rapide, plus efficace, plus précis et plus performant, que ce soit dans le sport ou dans un atelier de production.
Il a ce défi des challenges difficiles, qui se révèle d’autant plus qu’il y a de chiffres après la virgule ! La précision est certainement le terme qui caractérise le mieux Franck Boccaccini. Là où certains trouvent trouvent leurs limites dans l’approfondissement, dans le détail invisible, Franck trouve un nouvelle raison d’aller plus loin, de découvrir… Tout comme lorsqu’il part au bout du monde naviguer au milieu de vagues aussi hautes que son mât de planche à voile.
Cette perfection et cette précision, combinées à une analyse en temps réel des données en jeu font de lui un redoutable analyste industriel, un usineur hors pair et un conseiller en productique qui vous apportera des solutions et une productivité accrue.
Son parcours professionnel est impressionnant : à chaque fois qu’il me raconte l’importance de ses études, son implication personnelle et l’impact de ses solutions sur les différentes productions, je reste ébahit. Il a une façon de présenter des choses très compliquées de façon compréhensible au tout à chacun. Il transpire une telle passion dans ces récits qu’on est pris au jeu de cette précision, de son amour pour la matière, les détails, la qualité et cette recherche de la perfection.
Nul doute que Franck, récemment installé à son compte sera un atout précieux pour toute production qui souhaite réaliser un audit, améliorer sa productivité, former ses employés… Sans parler de son domaine de prédiction qui est l’horlogerie. Après 14 années passée à travailler à Genève, Franck est capable de mettre en place une manufacture horlogère complète !
En tant qu’ami, je dis bravo, car c’est un parcours professionnel hors normes pour quelqu’un qui a très tôt trouvé sa vocation : l’usinage et la productique.